Simulate to scale: Process simulation helps scale sustainable industry
Posted: May 16, 2025
Process simulation used to live in a silo—confined to isolated tasks in the oil, gas, and chemical industries, and limited to narrow phases of design. Today, however, it’s a catalyst for sustainable transformation. Engineers are now using advanced simulation tools across the entire plant life cycle to test, optimize, and scale low-carbon technologies—before a single pipe is laid or bolt is turned.[1]
With a platform-based approach, advanced process simulation software now extends far beyond process design. Engineers can design, test, and optimize industrial processes that are traditionally time- and resource-intensive—like chemical production, fuel and power generation, or hydrogen electrolysis—in a virtual environment that mirrors the real world.
As AVEVA’s Cal Depew puts it, the shift is as dramatic as the leap from flip phones to smartphones. In the past, we might have carried separate devices for music, photos, directions, games, and phone calls—now we have all of this integrated in a computer that fits into our pocket. Similarly, with advanced simulation software, process engineers have a single unified modeling environment to use across all engineering phases to explore all dimensions of a potential design.
Here’s how three companies across industries are using process simulation to scale sustainable innovation.
Covestro simulates processes for green polymer production
In the chemicals industry, process models that enable companies to test many different scenarios and make accurate predictions are helping create more cost-effective, less energy-intensive chemical processes.
Covestro, a global leader in polymers, has pledged to achieve Scope 1 & 2 net-zero emissions by 2035. To meet this goal, its engineers had to find less energy-intensive processes for polymer production. They also needed to include new recyclable materials and bio-based feedstocks in their production processes. But new processes of this kind are notoriously difficult to model, as they require aggregating complex and evolving thermodynamics and solid processing steps.

Covestro was already using process simulation software for its established processes. Because of the software’s flexibility, Covestro engineers can reuse existing models, working with the same molecules and materials to model new processes without having to build a model from scratch. This modeling allows them to create less energy-intensive methods, save time, and enables them to determine how to best produce their new green polymer at scale.
Topsoe scales production of electrolyzers for the green hydrogen revolution
Renewable energy production processes include a complex array of factors. Wind farms and solar panels are subject to the unpredictability of weather. Grid stability, fluctuating markets, and changing government regulations add even more complexity. Advanced process simulation helps model how intermittent renewable inputs—like solar or wind—can affect the operation and efficiency of clean hydrogen production systems.
Green hydrogen, for example, while a promising renewable energy source, can be challenging and expensive to produce. One factor that is currently stalling the widespread production of green hydrogen—hydrogen produced without CO2 emissions—is the current shortage of electrolyzers. The International Energy Agency says we are going to need to produce many more electrolyzers to meet future green hydrogen targets.[2]
Topsoe, a leader in carbon emission reduction technologies, is ramping up its production of a newer, more efficient solid oxide electrolyzer (SOEC). These more efficient electrolyzers make it possible to produce more hydrogen per unit of power, and by using renewable energy to power the electrolysis process, they enable emission-free conversion of water into hydrogen and oxygen. Topsoe’s SOEC electrolyzers deliver up to 30% more hydrogen from the same electricity volume at a 30% lower cost.
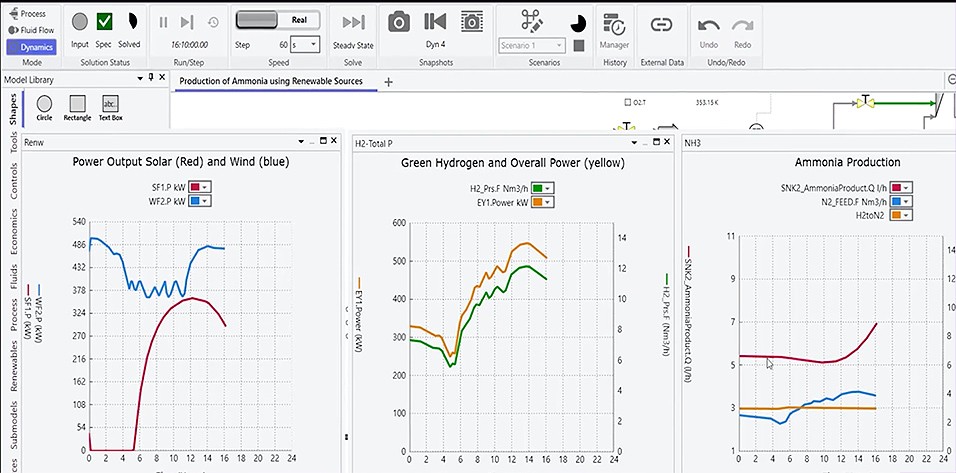
Legacy simulators typically separated process design from control strategy development, which often meant designing the system first, and then later building a separate model for control testing. This separation introduces errors and costs time and money. Using AVEVA™ Process Simulation, which can combine process design and control strategy within the same simulation environment, Topsoe can model how hydrogen is produced under various conditions, test configurations to get the best performance and efficiency, and understand the interactions between heat, electricity, and materials inside one simulation. This allows Topsoe to reduce the number of models needed, speed up the engineering and commissioning of new plants, and detect and solve issues early. Topsoe is currently building a gigafactory for electrolyzers—a massive, complex project that requires large-scale system modeling to help ensure the smooth integration of systems and processes.
ExxonMobil synthesizes new processes for renewable diesel production
Traditional oil and gas companies are also looking to develop new processes that meet the demand for fuel while committing to a more sustainable future. ExxonMobil plans to invest approximately $17Bn in lower-emission fuel initiatives by 2027. As Dr. Kirtan Trivedi of ExxonMobil explains, “Growing sustainable fuels is going to require a lot of new processes, and so the question becomes, how do I go about synthesizing that new process?”
To support this effort, ExxonMobil used AVEVA™ PRO/II™ Simulation—AVEVA’s legacy steady-state simulation tool—to design and evaluate a two-stage process of renewable diesel production that yields fuel with properties of conventional diesel. Steady-state simulation played a crucial role in helping the team identify the optimal conversion pathways, allowing ExxonMobil to refine paraffins into iso-paraffins efficiently— preserving fuel yield and improving performance in cold weather conditions.
Advanced process simulation speeds up a better tomorrow
Today, next-generation simulation platforms can help companies go beyond steady-state modeling. Advanced process simulation platforms like AVEVA Process Simulation support both steady-state and dynamic simulation within a single environment, allowing engineers to test, optimize, and scale low-carbon technologies across the entire process life cycle—from conceptual design to operations and control strategy development.

Given the uncertainties of climate change and the volatility of changing geopolitics and markets, organizations are looking at digital tools to help them do more with less. The unified modeling environment in AVEVA Process Simulation integrates cross-functional tools within a single platform. A smartphone for process engineers. What’s more—sustainability is built in. Greenhouse gas calculations, along with solar, wind, and hydrogen models are available in libraries. Open modeling means no specialist knowledge is needed. Advanced process simulation provides a way for companies to innovate new materials and processes with less time and resources. Whether it’s the discovery of a more sustainable polymer, more efficient green hydrogen production, or better renewable fuel, advanced process simulation software can help speed up a better tomorrow.
[1] Julien de Beer and Cal Depew. Computers & Chemical Engineering, Volume 154. (November 2021). The role of process engineering in the digital transformation. https://www.sciencedirect.com/science/article/abs/pii/S0098135421002015
[2] IEA. Electrolysers. Retrieved from < https://www.iea.org/energy-system/low-emission-fuels/electrolysers>.
Related blog posts
Stay in the know: Keep up to date on the latest happenings around the industry.